The Challenges Facing Battery Manufacturers
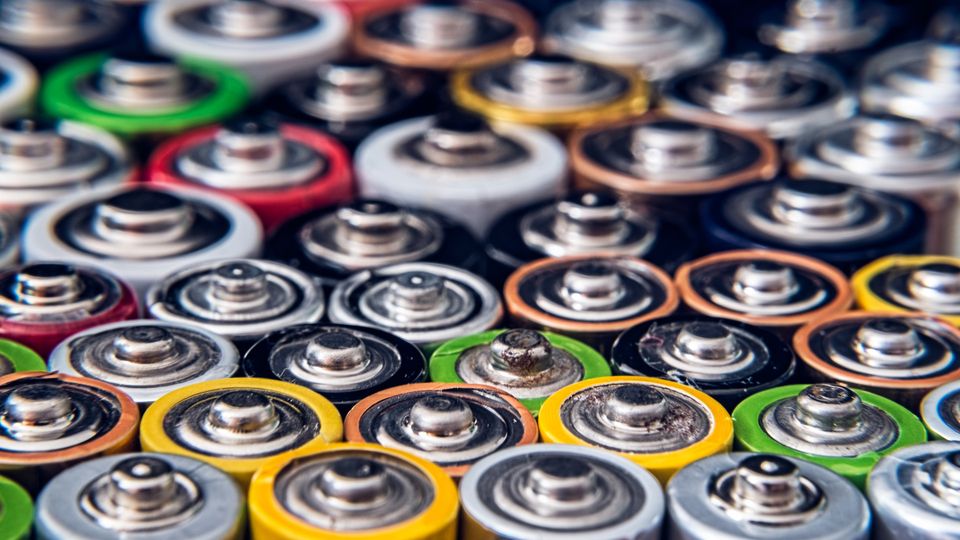
Complete the form below to unlock access to ALL audio articles.
Advanced lithium-based batteries have arguably never been in as high demand as they are today. Unfortunately, shortages affecting the rare earth metals needed for their production are throttling the ability of battery manufacturers to meet current demand.
Academic researchers have made significant strides toward developing alternate battery chemistries that could side-step these supply issues in recent years. But it is not uncommon for manufacturers to run into additional problems when attempting to scale up the production of these new battery materials for batch manufacturing. Between poor yields, impurities and other quality control issues, the discrepancy in challenges faced by academic versus industrial laboratories has been identified as a key area for focus for the future.
Researchers from the Pacific Northwest National Laboratory, Penn State University, the University of Washington, Mercedes-Benz and Thermo Fisher Scientific, recently authored a paper published in Nature Energy, bringing together their different viewpoints and specialties to review the challenges faced by manufacturers and strategize for new opportunities for future development.
To learn more about the challenges and opportunities involved in scaling up lithium-based battery production, Technology Networks spoke with Zhao Liu, senior market development manager at Thermo Fisher Scientific and one of the co-authors of the new paper.
Alexander Beadle (AB): Can you tell us about some of the current challenges battery manufacturers are facing?
Zhao Liu (ZL): Battery manufacturers are facing several challenges including cost, material shortages and safety issues as they work to develop and improve battery technology. While the cost of batteries has decreased over the years, cost still prohibits the widespread adoption of batteries. Manufacturers need to find ways to reduce the cost of raw materials, production and increase economies of scale to bring down the cost of batteries.
Battery manufacturers are challenged by an ongoing shortage of raw materials because of the increased demand for battery-powered devices as well as the complexity of the global supply chain. For example, critical elements such as cobalt – found primarily in the Republic of the Congo – are subject to supply shortages. To counter this, there has been a significant effort to design and produce batteries containing less cobalt in them, or even a completely cobalt-free battery.
These manufacturers work hard to ensure battery safety. Safety recalls are expensive for both original equipment manufacturers and cell manufacturers. To address this challenge, improved quality assurance is key. The quality of the battery must be monitored through every stage of the manufacturing process. This requires significant metrology development. For example, metal impurity is a key factor that causes battery performance to degrade and there is not yet an effective solution to detect impurities throughout the entire cell manufacturing process, from raw materials to a final cell.
AB: Why is scale-up particularly problematic?
ZL: In our recent paper published together with national labs, universities and industry leaders, we took an in-depth look at the challenges that occur when transferring the knowledge gained from the lab to battery manufacturing at scale. There are many blind spots in terms of yields, impurities and quality control that occur when materials research is scaled up to industry manufacturing levels.
In the laboratory environment, you can easily synthesize high-performance materials at a small batch size (for example, at 1 gram). However, when you try to scale up to a large batch size (e.g., 0.1 kg to thousands of kilograms) in manufacturing, challenges such as homogeneous mixing and the formation of non-stoichiometric byproducts start to impact the quality of the final product. In this case, different materials processing strategies are needed for large batch samples to ensure the performance of the materials synthesized at scale.
AB: How can academia and industry work together to address some of these issues?
ZL: The key is to ensure that academia is also working to address industry challenges. In our recent paper, we highlight the need for academia to dedicate research to address challenges associated with scaling up and moving lab materials to the manufacturing environment.
Metal impurity is a big challenge for battery production but the tolerance level of impurities in the industrial environment is not yet understood. However, in academic research, impurity is not commonly considered a key factor for battery performance evaluation. There is a knowledge gap in materials research in this space. If academia were to focus research on how to reduce the impurities during the materials synthesis and production process and how to develop effective metrology to detect those impurities, the production quality of batteries could be improved.
AB: In what ways can materials science be used to ensure battery performance and safety?
ZL: Materials science is essential in ensuring battery performance and safety, which are dependent both on the materials and structure of the materials used to construct the battery. The properties of the materials themselves determine the performance and safety of a battery cell. In batteries, there are often two approaches – either safer material or a material with a more energy-optimized structure. The use of lithium nickel manganese cobalt oxide (NMC) and lithium iron phosphate (LFP), two common cathode materials in electric vehicles, serves as an example. NMC delivers higher specific energy density and has a shorter life cycle, but LFP is safer, with inferior energy performance. Depending on the cell performance requirement, different materials need to be selected and optimized. Materials science helps guide us to determine which materials we should select.
Additionally, structurally the battery itself is quite a complex electrochemical system. The microstructure characteristics from millimeter to atomic scale can impact battery performance. Thus, how to characterize the structure of the battery is critical. Our recent research further explores the characterization needs in materials development and manufacturing, which enables quality assurance for high-quality battery manufacturing. Specifically, the use of electron microscopes helps us understand the battery structure in multi-dimension and multi-length scale and correlate it with battery performance. The designed battery-specific workflow is highly desirable and can facilitate efficiency and accuracy in obtaining critical structure information for better battery development and more efficient production.
AB: What do you see in store for the future of battery development and manufacturing?
ZL: In battery development, new battery chemistries with better performance, lower cost, and enhanced safety are the future. Innovations such as solid-state batteries and lithium–sulfur batteries could replace current-generation lithium-ion batteries. They are safer, have a higher energy density, and can be produced at a lower cost.
In battery manufacturing, we see more investment in automated innovation. Traditionally, battery manufacturing can involve many manual and labor-intensive steps such as assembly, cell testing and quality control. Automated innovation aims to minimize human error and increase efficiency by automating these processes. In our recent paper, we discussed how smart manufacturing, like digital twin technology, provides a feedback loop between simulated data and the real manufacturing process via artificial intelligence and how it can effectively optimize the manufacturing process and improve yield.
Additionally, enhanced automation in the metrology process during manufacturing will make battery production more efficient and cost-effective. The current impurity metrology process in battery cell manufacturing is labor-intensive, and the entire process from sample preparation to final data analysis and reporting takes hours, which significantly impacts the efficiency of cell production and ultimately can become very expensive.
As battery demand continues to grow, it also becomes increasingly important to find sustainable solutions for battery disposal. The recycling and reuse of batteries will play a significant role in reducing the environmental impact of battery production and use, as well as helping combat the shortage of raw materials. Ultimately the future of battery development and manufacturing is exciting and looks promising, with significant advancements on the horizon that will result in safer, more efficient and more sustainable energy storage solutions.
Zhao Liu was speaking to Alexander Beadle, Science Writer & Editor for Technology Networks.