Producing Green Steel from Toxic Industrial Waste
A new hydrogen plasma-based reduction process could turn toxic red mud into iron that is pure enough for steelmaking.
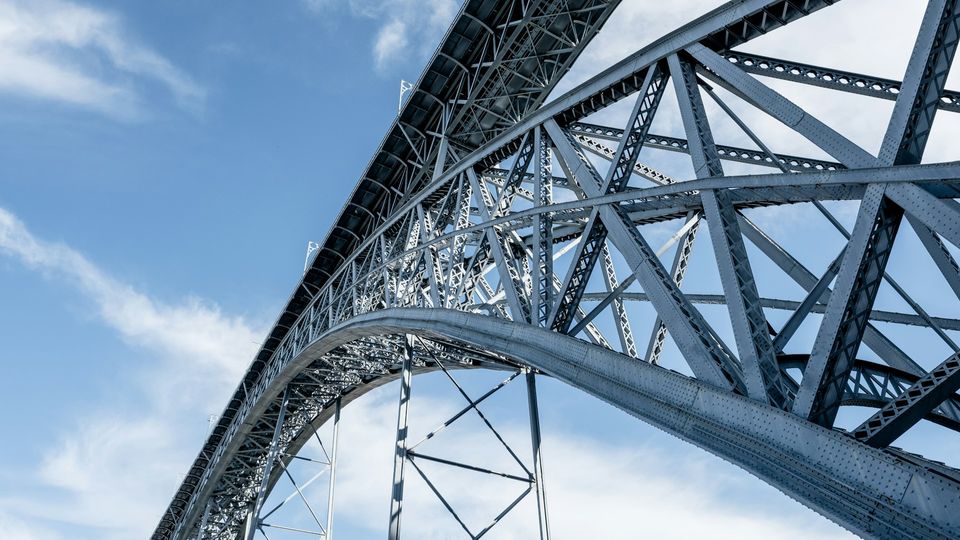
Complete the form below to unlock access to ALL audio articles.
Aluminum is an extremely in-demand material, used for everything from building materials to food packaging. But its production also creates an estimated 180 million metric tons of corrosive, toxic “red mud” industrial waste each year.
Now, researchers from the Max Planck Institute for Iron Research (MPIE) have developed a new method for processing this waste, which extracts significant amounts of high-quality iron from the mud that can be used directly in steelmaking.
Wide adoption of this new hydrogen plasma-based reduction process could help to slash the environmental impact of both the aluminum and steelmaking industries, the researchers say.
The research is published in Nature.
The impacts of red mud
The steel and aluminum industries are in their ascendency, with the International Aluminium Institute (IAI) estimating that global aluminum demand could increase by almost 40% by 2030.
However, the traditional production of these two materials has a significant impact on the environment. Steel production creates as much as ~eight percent of global carbon dioxide emissions. For its part, the aluminum industry produces huge volumes of red mud – a highly alkaline byproduct of the Bayer process used to produce alumina from ore.
This red mud is mostly made up of various metal oxides, but it also contains traces of dangerous heavy metals. This waste is normally disposed of by drying it out, then containing it in large landfill sites. During heavy rain, the red mud can be washed out of the landfill and spill into the environment. Its highly alkaline nature can also begin to attack the concrete walls of the landfills it is contained in, resulting in large-scale environmental disasters when the walls are breached – as seen with the alumina plant accident that occurred near the Hungarian town of Ajka in 2010.
Red mud gets its distinct color from its high iron oxide content. Knowing this, the researchers set out to discover if there is an economically viable way to pull the iron out of the red mud – circumventing the carbon dioxide-intensive processes normally used in iron production – while also treating the aluminum waste to make it less corrosive.
"Our process could simultaneously solve the waste problem of aluminum production and improve the steel industry's carbon footprint," said the study’s first author Dr.-Ing. Matic Jovičevič-Klug, a postdoctoral researcher at the MPIE.
Turning mud into steel
The solution the MPIE team came up with uses an electric arc furnace, similar to those that are already used widely in the steel industry. Feeding the furnace with a lean mixture of hydrogen and argon gas, and igniting it with a 200 amp electrical discharge, creates a plasma containing roughly 10% hydrogen. This plasma melts the red mud inside the furnace while simultaneously reducing any iron oxide to metallic iron.
This process, known as plasma reduction, takes just 10 minutes and effectively separates the liquid iron from the other liquid oxides. After repeating the procedure 6 times, the researchers were able to extract 98% of the theoretical limit from their test sample; equating to 2.6 grams of metallic iron from 15 grams of red mud. The resulting iron metal was found to be pure enough that it could be immediately used in steelmaking.
Subscribe to Technology Networks’ daily newsletter, delivering breaking science news straight to your inbox every day.Want more breaking news?
The new process also rendered the remaining metal oxides in the red mud non-corrosive. Upon cooling, they solidified into a glass-like material that the researchers say could be used as a filling material in the construction industry, for example. The heavy metals in the red mud were also effectively neutralized, becoming firmly bound either within the other metal oxides or as an additive to the iron.
“After reduction, we detected chromium in the iron," said Jovičevič-Klug. "Other heavy and precious metals are also likely to go into the iron or into a separate area. That's something we'll investigate in further studies. Valuable metals could then be separated and reused."
Is the process realistic?
The idea of pulling usable iron out of red mud is something that has been proposed before; previous groups have investigated doing this using carbon in the form of coke. However, the iron produced from these processes contains more impurities and still produces large volumes of carbon dioxide (CO2). With their new process, which can also be fueled by green hydrogen produced using renewable electricity, the researchers say they have created a more environmentally friendly process.
"If green hydrogen would be used to produce iron from the four billion tons of red mud that have been generated in global aluminum production to date, the steel industry could save almost 1.5 billion tons of CO2," said Dr. Isnaldi R. Souza Filho, research group leader at the MPIE.
More than just benefitting the environment, the researchers’ cost analysis suggests that the technique could make economical sense too. Using hydrogen and electricity from partially-renewable sources, the researchers calculate that the process would be worthwhile if the red mud contains more than 50% iron oxide or more. Taking into account the costs associated with disposing of red mud, this process could be competitive on the market for red mud containing just 35% iron oxide.
"These are conservative estimates because the costs for the disposal of the red mud are probably calculated rather low," added Souza Filho.
With electric arc furnaces already being widely used in the metal industry, many operators would only need to invest a small amount in order to adopt this new process. Securing sources of green hydrogen and renewable energy may take more work, however.
"It was important for us to also consider economic aspects in our study," said Prof. Dr.-Ing. Dierk Raabe, director of the MPIE "Now it's up to the industry to decide whether it will utilize the plasma reduction of red mud to iron."
Reference: Jovičević-Klug M, Souza Filho IR, Springer H, Adam C, Raabe D. Green steel from red mud through climate-neutral hydrogen plasma reduction. Nature. 2024;625(7996):703-709. doi: 10.1038/s41586-023-06901-z
This article is a rework of a press release issued by the Max Planck Institute for Iron Research. Material has been edited for length and content.