New Kinds of Padding Could Make Football Gear, Bike Helmets Safer Than Ever
A 3D-printed foam material with an almost honeycomb-like structure could enhance the protection offered by helmets.
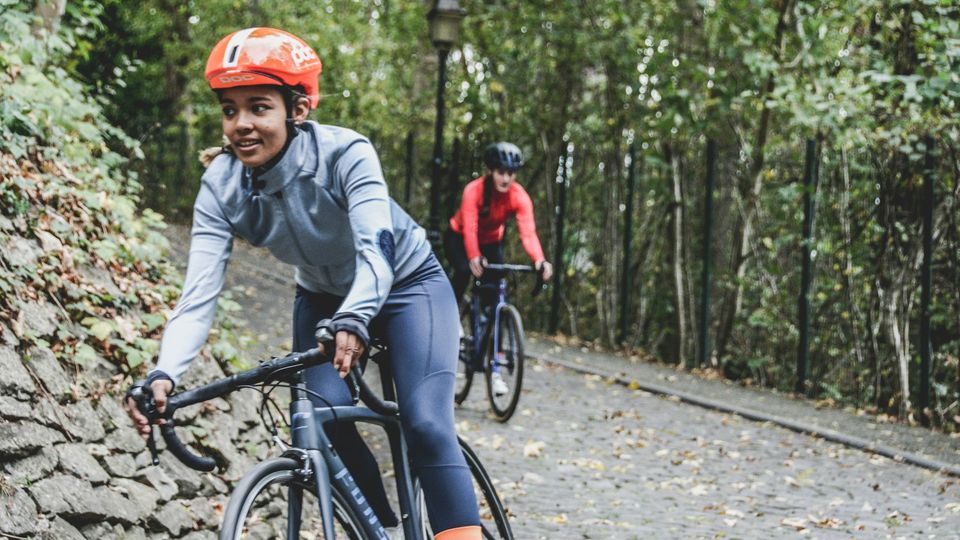
Complete the form below to unlock access to ALL audio articles.
Football players (and anyone else who takes hard hits) may want to breathe a sigh of relief.
In recent research, engineers at the University of Colorado of Boulder and Sandia National Laboratories have developed a new design for padding that can withstand big impacts. The team’s innovations, which can be printed on commercially available 3D printers, could one day wind up in everything from shipping crates to football pads—anything that helps to protect fragile objects, or bodies, from the bumps of life.
The team described the technology in January in the journal “Advanced Materials Technologies.”
“Impact mitigation is something that’s important everywhere,” said Robert MacCurdy, corresponding author of the study and assistant professor in the Paul M. Rady Department of Mechanical Engineering at CU Boulder. “It’s in highway crash barriers, knee pads and elbow pads, and in packaging equipment.”
Want more breaking news?
Subscribe to Technology Networks’ daily newsletter, delivering breaking science news straight to your inbox every day.
Subscribe for FREEHe and his colleagues think they can do better.
In the new study, the group wrote computer algorithms to meticulously redesign the interior of cushioning materials—allowing them to buckle under force, but only following a careful pattern. When the group put their designs to the test in the lab, they discovered that their padding could absorb as much as 25% more force than current state-of-the-art technologies.
“The material you use for absorbing impacts matters,” MacCurdy said. “But what really matters is the geometry.”
Zooming in
To understand why some cushions work well, and others don’t, it helps to look deep inside.
What gives a foam its spring, for example, are all those little nooks and crannies. When you squeeze a sponge, MacCurdy explained, those empty spaces will begin to close up, which, in turn, absorbs energy.
Some engineers have moved beyond that basic design. Instead, they make padding out of a network of towers, or “plate lattices,” that look a bit like honeycombs. If a linebacker, perhaps, crashes into this kind of cushion, the impact will cause the honeycombs to collapse in a wave-like pattern. That’s a more efficient way to absorb forces.
But, MacCurdy noted, researchers have long strived for padding that meets a gold standard— technology that doesn’t just absorb a lot of force, but can also absorb many different kinds of forces with the same finesse.
“If you’re riding your bike and get into a crash, you don’t know if that’s going to be a low-speed impact or a high-speed impact. But regardless, you expect your helmet to perform well,” he said. “We’re trying to develop a geometry that performs well under all of those scenarios.”
Giving the squeeze
To make a more versatile cushion, the engineer and his colleagues opted to rearrange the interior of these objects, down to the scale of a millimeter or less.
The group first used custom software to lay out a network of honeycombs, then tweaked them to include a few kinks, a bit like the bellows in an accordion. Those kinks help to guide the honeycombs as they crunch down during an impact, allowing for a much smoother collapse.
“The moment you start to compress these structures, they absorb a certain amount of force,” MacCurdy said. “The best absorber designs maintain a constant force across the whole range of compression.”
In other words, unlike a foam, these cushions will behave the same no matter how much you squish them down—or, at least, up to a certain maximum.
The researchers also wanted to make sure their padding could stand up to bumps and bruises in the real world. They used a 3D printer to create blocks the size of a small brick out of a springy material called thermoplastic polyurethane. Then they squeezed them with an impact-testing machine.
The group discovered that its blocks could absorb roughly six times more energy than standard foams made out of the same material, and up to 25% more than other honeycomb designs. MacCurdy and his colleagues are currently working to improve on their structures even further. He added that engineers can make these kinds of designs out of many different types of materials, from bouncy plastics to harder substances like aluminum.
The world, in other words, could soon be a much softer place.
Reference: Smith L, Hayes B, Ford K, Smith E, Flores D, MacCurdy R. Tunable metamaterials for impact mitigation. Adv Mater Technol. 2024:2301668. doi: 10.1002/admt.202301668
This article has been republished from the following materials. Note: material may have been edited for length and content. For further information, please contact the cited source.